Thermoplastic extruder pumps
Thermoplastic extruder pumps (melt gear pumps) are widely used in the extrusion industry, and their application scope covers multiple fields, as detailed below:
Plastic Products Production
Sheet, Plate, and Pipe Production: During the production of sheets, plates, and pipes, a thermoplastic extruder pump can be installed between the extruder outlet and the die, serving as a melt metering pump. It can significantly improve the stability of the die pressure, achieve a nearly linear output of the flow rate, thereby ensuring the dimensional accuracy and surface quality of the products, increasing the output, reducing the load on the extruder, and saving energy and costs.
Film Production: In film extrusion production, a thermoplastic extruder pump can steadily convey high-temperature plastic melts, ensuring uniform film thickness and improving product quality. Its optimized melt flow channel design can eliminate dead zones, reduce polymer residues, and further enhance the performance of the film.
Fiber (Drawing) Production: In plastic drawing production, a thermoplastic extruder pump can precisely control the flow rate and pressure of the melt, resulting in filaments with uniform diameters and smooth surfaces, meeting the requirements for producing high-quality fiber products. At the same time, it can quickly respond to changes in process parameters to maintain the stability of the drawing process.
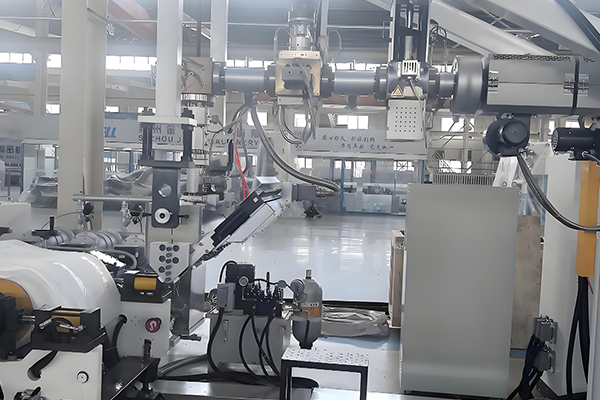
Rubber Products Production
In the rubber industry, thermoplastic extruder pumps can be used to produce various rubber products, such as tires, rubber belts, and sealing strips. They can adapt to the high-viscosity characteristics of rubber melts, achieve stable extrusion and conveyance, and ensure the quality and production efficiency of rubber products.
Co-extrusion and Compounding
Co-extrusion Production: In the co-extrusion process, a thermoplastic extruder pump can simultaneously handle multiple different melts, precisely control the flow rate and pressure of each layer of melt, realize the stable extrusion of multi-layer composite materials, and meet the performance requirements of different products.
Compounding and Pelletizing: In a compounding and pelletizing production line, the use of a twin-screw extruder in conjunction with a thermoplastic extruder pump can improve the compounding quality and output, reducing energy consumption by approximately 25%. The thermoplastic extruder pump can pressurize and stabilize the melt after compounding, ensuring the uniformity and stability of the pellets.
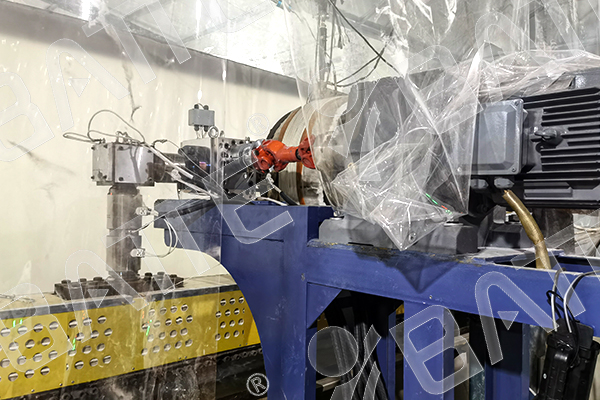
Precision Extrusion Field
Thermoplastic extruder pumps are suitable for precision extrusion systems. Their extremely low pressure and flow rate pulsations and high precision can meet the production requirements for products with high dimensional accuracy and surface quality, such as synthetic fibers for high-end textiles and optical-grade films.
Special Operating Conditions Applications
Thermoplastic extruder melt pumps can be applied under high-temperature (≤350℃), high-pressure (0 - 40MPa), and high-viscosity (0.001 - 40000Pa·s) conditions. There are also multiple wear-resistant configurations and sealing methods available for selection. They are suitable for high-filling conditions and applicable to both electric heating and heat medium heating.
Email: sale@meltpump.com
WhatsApp: +86 158 38331071