What types of materials can a rubber extruder melt pump handl
The rubber extruder melt pump can handle a diverse range of materials, encompassing various polymer materials and special industrial substances, which can be specifically categorized as follows:
Rubber and Elastomer Materials
General Rubbers:
Natural rubber (NR), styrene-butadiene rubber (SBR), butadiene rubber (BR), chloroprene rubber (CR), nitrile rubber (NBR), ethylene propylene diene monomer rubber (EPDM), etc. Application Scenarios: Extrusion molding of tire treads, rubber hoses, sealing strips, shoe materials, etc. The melt pump stabilizes pressure fluctuations (within ±1%), enhancing the dimensional accuracy of products (e.g., wall thickness deviation of medical catheters ≤ 0.02mm).
Special Elastomers:
Thermoplastic polyurethane elastomers (TPUR), fluoropolymers, polysulfones, etc. Technical Adaptability: Adopts a mirror-finish flow channel design (surface roughness Ra ≤ 0.2μm) and an end-shaft cooling system to prevent degradation of thermally sensitive materials, supporting high-temperature operations up to 400°C.
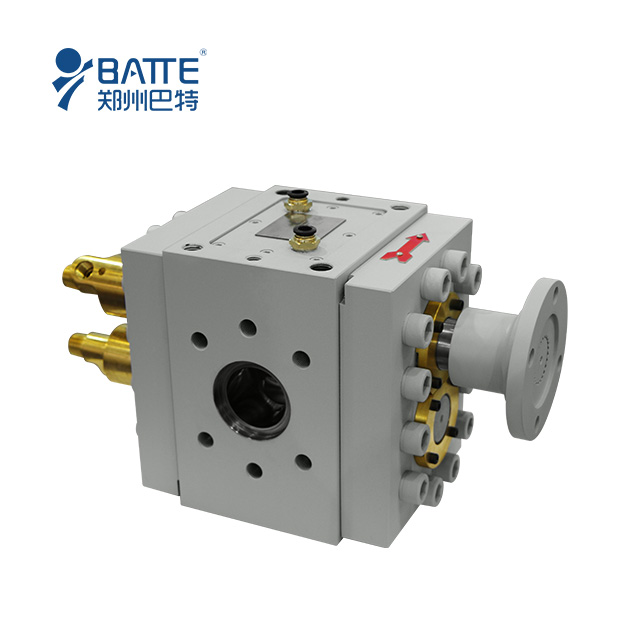
Plastic and Resin Materials
General Plastics:
Polyethylene (PE), polypropylene (PP), polyvinyl chloride (PVC), polystyrene (PS), high-impact polystyrene (HIPS), polycarbonate (PC), polyamide (PA), etc.
Application Scenarios: Extrusion production of pipes, sheets, films (e.g., reducing BOPP film thickness deviation from 5% to 1%), wood-plastic profiles (PVC + wood powder), etc.
Engineering Plastics:
Polyethylene terephthalate (PET), polyoxymethylene (POM), polyphenylene sulfide (PPS), polyether ether ketone (PEEK), polyimide (PI), etc.
Technical Adaptability: Supports high-pressure operations (outlet pressure 40MPa, pressure differential 25MPa), meeting the demands of high-end products (e.g., elevating the temperature resistance of aircraft engine components to 320°C).
Modified Plastics:
Glass fiber-reinforced plastics (e.g., glass fiber-reinforced PA66), chemically recycled regenerated materials (e.g., narrowing the melt index fluctuation range of HDPE from ±15% to ±3%).
Technical Adaptability: Achieves micron-level flow control through a five-gear melt pump, supporting the development of functional textiles (e.g., flame-retardant, antibacterial fibers).
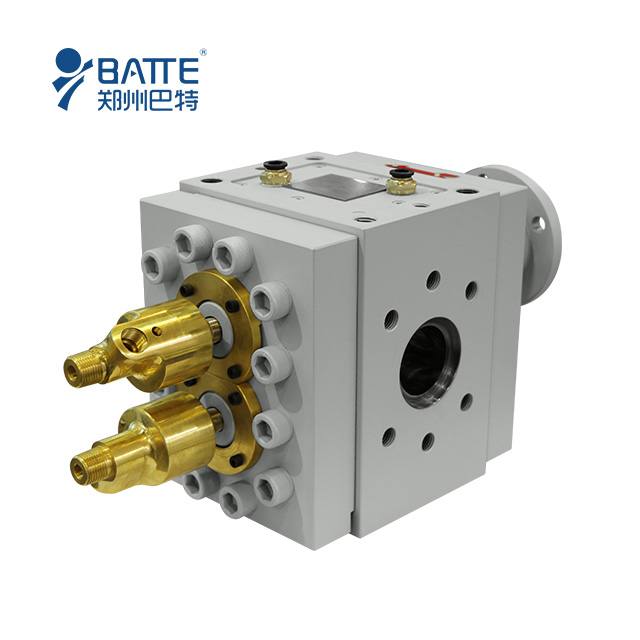
Chemical Fiber and Fiber Materials
Melt Spinning:
Polyester (PET), nylon (PA6/PA66), artificial fibers, optical fibers, etc.
Technical Adaptability: Stably conveys high-temperature melts above 300°C, reducing the irregularity rate of single filament fineness from 2.5% to 0.8% and decreasing spinning breakage rates by 40%.
Wet Spinning:
Battery separator materials (e.g., polyethylene/paraffin mixtures).
Technical Adaptability: Controls microporous structures with ±0.5% precision, enhancing separator puncture strength from 300g/μm to 500g/μm and achieving a pass rate exceeding 95%.
Special Industrial Materials
Low-Viscosity Fluids:
Hot-melt adhesives, asphalt, paints, adhesives, dyes, coatings, lubricants, polyols, etc.
Technical Adaptability: Automatically compensates for feed fluctuations through a PID algorithm, maintaining stable flow rates (e.g., ±0.5% flow accuracy in coating production).
Environmental and Recycled Materials:
Recycled HDPE, chemically recycled PET depolymerization liquids, etc.
Technical Adaptability: A two-stage melt pump system homogenizes viscosity fluctuations in recycled materials, improving recycling efficiency and reducing energy consumption (overall energy consumption reduced by 30%-50%).
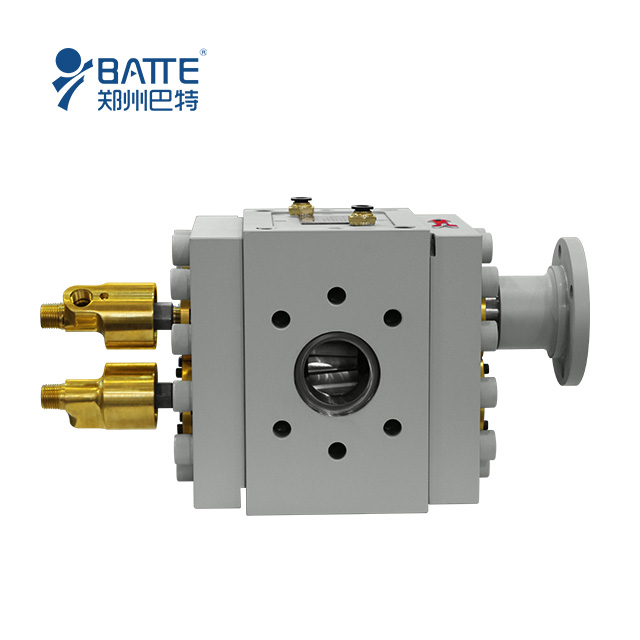
Emerging Field Materials
3D Printing Consumables:
PLA, ABS, TPU, and other 3D printing filaments.
Technical Adaptability: A miniature melt pump resolves issues of unstable long-distance wire feeding, increasing printing speed by 50% while enhancing interlayer bonding strength by 30%.
Metal 3D Printing:
Mixtures of metal powders and polymer binders.
Technical Adaptability: Gear components utilize metal 3D printing technology, enabling the melt pump to withstand pressures exceeding 100MPa and expanding applications in the aerospace sector.
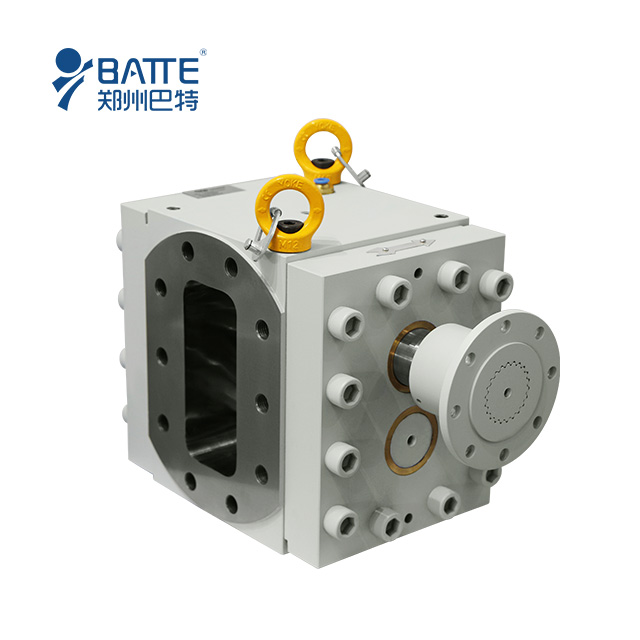
Technical Parameter Support:
Viscosity Range: 1–40,000Pa·s (1,000–40,000,000cP), covering a wide range from low-viscosity coatings to high-viscosity rubber (40,000Pa·s).
Pressure Range: Inlet pressure 0–30MPa, outlet pressure 0–40MPa, pressure differential 25MPa, adapting to high-pressure operations.
Temperature Control: Operating temperature ≤ 350°C, supporting high-temperature material processing (e.g., PEEK withstands temperatures up to 400°C).
Self-Cleaning Function: Optimized flow channels and lubrication systems eliminate residue and dead zones, extending equipment lifespan by 3-5 years.
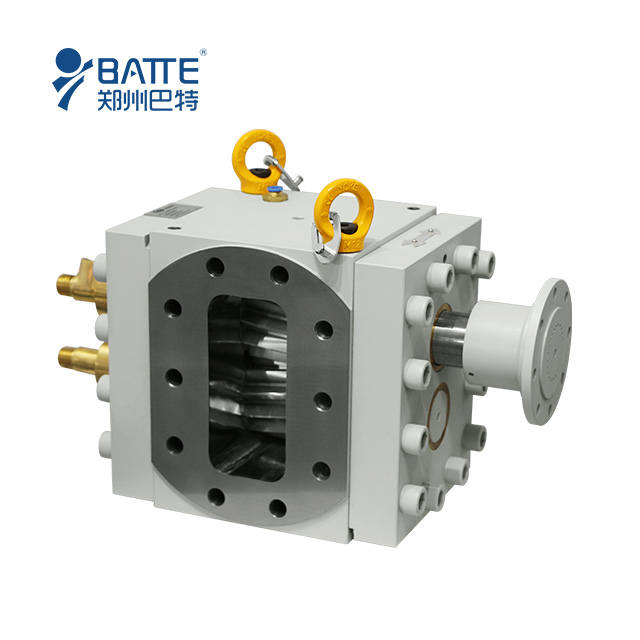
Summary: Leveraging its high-pressure, precision, and high-temperature resistance characteristics, the rubber extruder melt pump has become an indispensable core device in the rubber, plastic, chemical fiber, environmental protection, and emerging material sectors, driving modern industry towards efficient, stable, and green development.
Email: sale@meltpump.com
WhatsApp: +86 158 3833 1071